Petrophysical Training
Licenses
|
PRESSURE CONTROL BASICS
Portions of this page are from Petroleum Engineer's Handbook
(PEH) online version.
Pressure control during wireline operations,
such as perforating and production logging, is critical to
the health and safety of workers at the wellsite nearby
residents, domestic animals, and wildlife, not to mention
the nearby environment and the financial health of the oil
company and its executives and shareholders. Government
regulations and engineering best-practices keep failures to
a minimum, bur a few blowouts and gas leaks hit the evening
news often enough to suggest that someone messed up
somewhere.
This page describes the basic equipment and terminology
related to pressure control at the well.
The pressure control employed during wireline operations is intended
to contain pressure originating from the wellbore. During open hole
operations, the pressure might result from a well-kick. If
serious, the blowout preventer (BOP) would he closed, severing the
wireline and dropping the logging tools to bottom of the hole.
Heavier mud would be pumped in through the kill-line. With the well
stabilized, the BOP would be opened and the wireline and tools fished
from the borehole. Logging would resume and the well completed,
suspended, or abandoned.
During cased hole wireline work, the well may be capable of
producing at high pressure, either during or immediately after the
wireline procedure. A fair amount of research and planning is needed
to be sure the correct equipment is in place and tested before
trying to run the job.
PRESSURE CONTROL EQUIPMENT
This equipment starts with a connection to the top of the casing,
which forms the foundation for a semi-permanent fixture called the
well head. This is the control system during normal production,
and consists
of pipes, joints, valves, chokes, and pressure gauges
or sensors.
Additional equipment is added to the top of the well head during
wireline operations in cased holes..
Well head pressure control equipment must be rated to well over the
expected well-head pressure. Normal ratings for wireline pressure
control equipment is 5,000, 10,000, 15,000, and 20,000 psi.
The well head is also called well
head assembly, well head stack, or
“Christmas tree”.
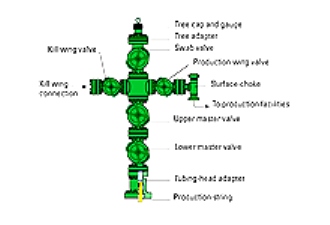
Cut-away view of a typical well
head (left) and "Christmas tree" style well head (right).
Schlumberger images
The following describes the components of the equipment added to the
well head temporarily to allow safe wireline operations in cased
holes. They are listed in order from top of well head upward to top
of final assembly. This material is from Wikipedia and
Schlumberger Glossary, edited for clarity.
Flange
A flange attaches to the top of the
well head assembly, usually with some sort of adapter for the rest
of the pressure control. A metal gasket is placed between the top of
the well head and the flange to seal against well pressure.
Quick-connect sub
A subassembly device that is bolted to
the top of the BOP stack that is designed to eliminate traditional
bolt-flanges to connect lubricator heads and utilize tapered-wedge
and lock ring designs. This allows the same security of traditional
pressure control connections
Tool trap
A tool trap has the same purpose as a head catcher
in that it prevents the tools from inadvertently dropping down the
hole. This device is normally located just above the well control
valves, providing protection to these important barriers from a
dropped tool. The tool trap has to be open in order to allow the
tools to enter the well, and is normally built to allow tools to be
recovered through the tool trap even when it is in the closed
position.
Wireline valve
A wireline control valve, also
called a wireline blowout preventer (BOP), is an enclosed device with
one or more rams capable of closing over the wireline in an
emergency. A dual wireline valve has two sets of rams and some have
the capability of pumping grease in the space between the rams to
seal against well pressure.
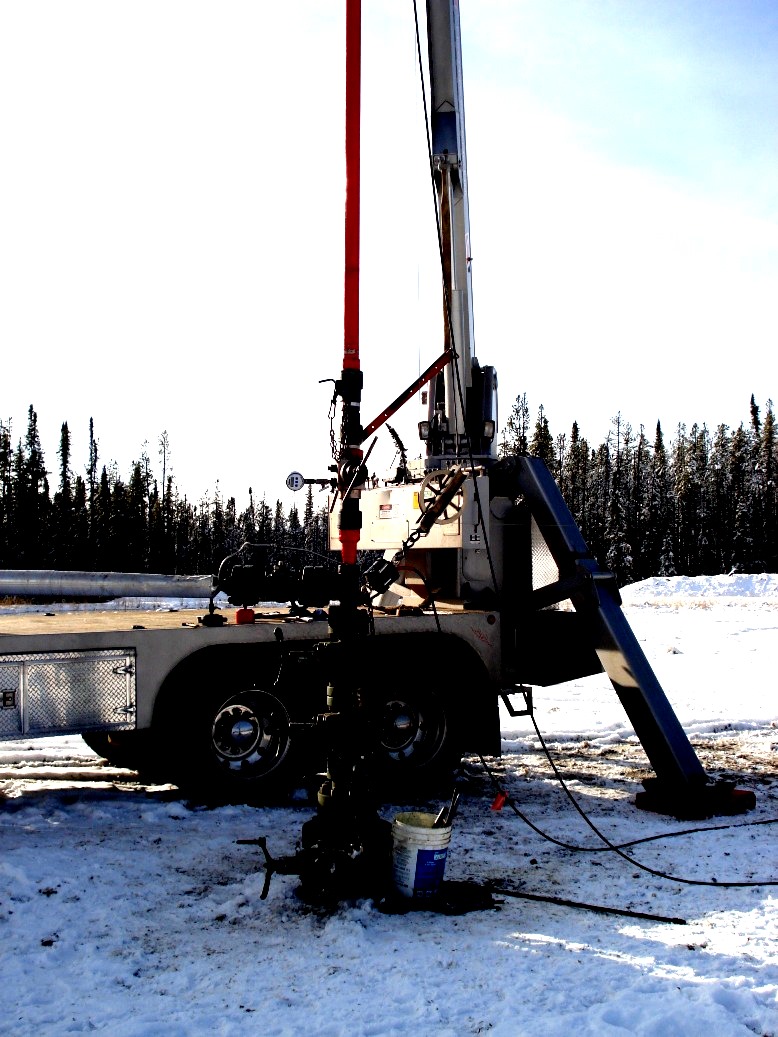
Lubricator
The lubricator
is a high strength,
pressure tested,
pipe fitted above the
wireline BOP
that allows tools to be put into a high pressure
well. The top of the lubricator assembly includes a high pressure
grease-injection section and sealing elements. The tools are placed
in the lubricator and the lubricator pressurized to wellbore
pressure. Then the top valves of the well head are opened to enable
the tools to fall or be pumped into the wellbore under pressure. To
remove the tools, the reverse process is used: the tools are pulled
up into the lubricator under wellbore pressure, the well head valves
are closed, the lubricator pressure is bled off, and then the
lubricator may be opened to remove the tools.
Pump-in sub
Pump-in subs, also called a flow-tee, allow for
the injection of fluid into the pressure control string. Normally
these are used for wellsite pressure testing, which is typically
performed between every run into the well. They can also be used to
bleed off pressure from the string after a run in the well, or to
pump in kill fluids to control a wild well.
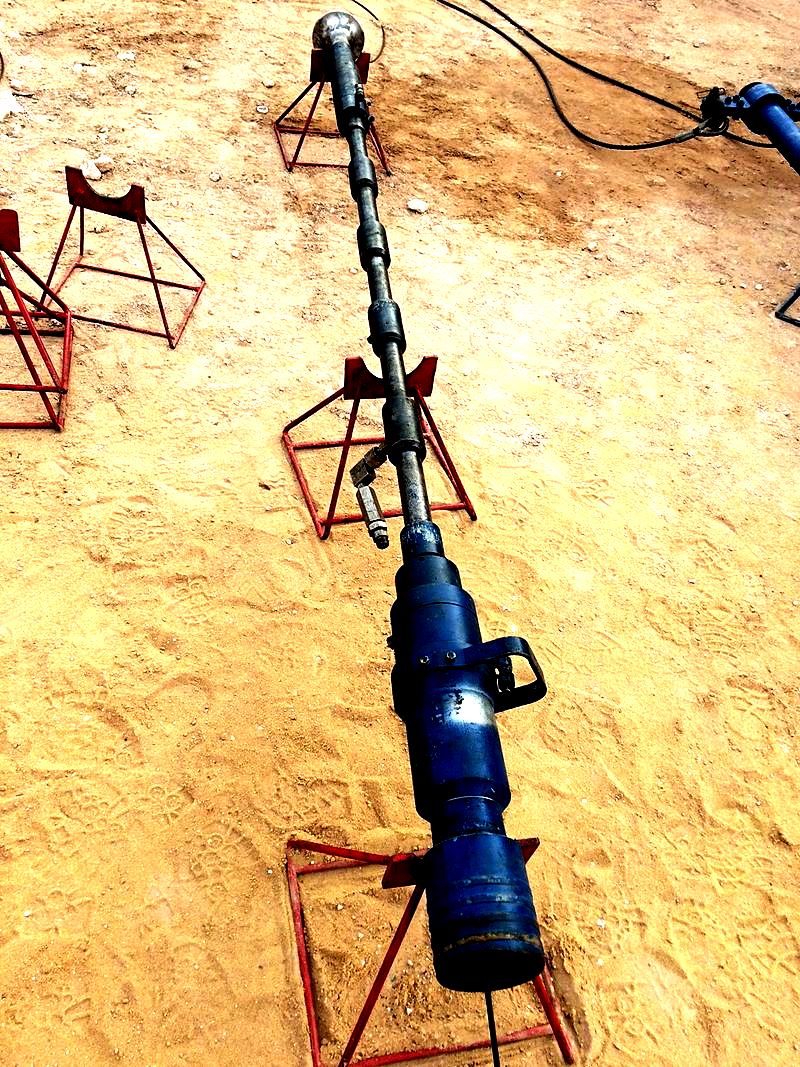
Grease injector head
The grease injector head is an assembly
of components used to contain wellhead fluids and pressure during
wireline operations. The wireline passes through a close-tolerance
tube assembly as it moves. High-pressure grease is pumped into the
surrounding annulus to effect a pressure-tight dynamic seal that is
maintained during the operation by injecting more grease as
required. A slight leakage of grease is normal, and the addition of
fresh grease ensures the seal is maintained.
Pack-off subs
Pack-off subs utilize hydraulic pressure on a
two brass fittings which compress a rubber sealing element to create
a seal around the wireline. Pack-offs can be hand pumped or
compressed through a motorized pumping unit.
Line wiper
A line wiper operates in much the same
way as a pack-off sub, except that the rubber element is
much
softer. Hydraulic pumps exert force on the rubber element until a
light pressure is exerted on the wireline, cleaning grease and well
fluid off the line as it moves past the wiper.
Ball check valve
If the wireline were to become severed
from the tool, a ball check valve can seal the well off from the
surface. During wireline operations, a steel ball sits to the side
of a confined area within the grease head while the cable runs in
and out of the hole. If the wireline exits that confined area under
pressure, the pressure will force the steel ball up toward the hole
where the wireline had been. The ball's diameter is larger than that
of the hole, so the ball effectively seals off pressure to the
surface.
Head catcher
A head catcher, also called tool
catcher, is a device placed at the top of the lubricator section.
Should the wireline tools be forced into the top of the lubricator
section, the head catcher, which looks like a small claw, will clamp
down on the fishing neck of the tool. This action prevents the tools
from falling downhole should the line pull out of the
rope socket. Pressure is applied to the head catcher to release the
tools.
|
|