CEMENTING
BASICS
This page describes cement bond logs
profiles, in the order of their appearance over the years.
This presentation style provides insights into tool
evolution, and a specific tool’s capabilities and
limitations. You will find most these tool types in your
well files – here’s your chance to learn more about them.
Cement
bond logs were run as early as 1958 with early sonic logs and the
temperature log was used to find cement top beginning in 1933.
Cement integrity logs are run to determine the quality of the
cement bond to the production casing, and to evaluate cement fill-up
between the casing and the reservoir rock. A poor cement bond
may allow unwanted fluids to enter the well. Poor fill-up of cement
leaves large channels behind the pipe that, likewise, allow the
flow of unwanted fluids, such as gas or water into an oil well.
By-products of cement integrity logs are the compressive strength
of the cement, the bond index, and in some cases, the quality
of the casing string itself.
Both
poor bond and poor fill-up problems can also allow fluids to flow
to other reservoirs behind casing. This can cause serious loss
of potential oil and gas reserves, or in the worst case, can cause
blowouts at the wellhead. Unfortunately, in the early days of
well drilling, cement was not required by law above certain designated
depths. Many of the shallow reservoirs around the world have been
altered by pressure or fluid crossflow from adjacent reservoirs
due to the lack of a cement seal.
Getting
a good cement job is far from trivial. The drilling mud must be
flushed out ahead of the cement placement, the mud cake must be
scraped off the borehole wall with scratchers on the casing, fluid
flow from the reservoir has to be prevented during the placement
process, and the casing has to be centralized in the borehole.
Further, fluid and solids loss from the cement into the reservoir
has to be minimized.
Gas
percolation through the cement while it is setting is a serious
concern, as the worm holes thus created allow high pressure gas
to escape up the annulus to the wellhead - a very dangerous situation.
Poor
bond or poor fill-up can often be repaired by a cement squeeze,
but it is sometimes impossible to achieve perfect isolation between
reservoir zones. Gas worm holes are especially difficult to seal
after they have been created.
Poor
bond can be created after an initial successful cement job by
stressing the casing during high pressure operations such as high
rate production or hydraulic fracture stimulations. Thus bond
logs are often run in the unstressed environment (no pressure
at the wellhead) and under a stressed environment (pressure at
the wellhead).
Cement
needs to set properly before a cement integrity log is run. This
can take from 10 to 50 hours for typical cement jobs. Full compressive
strength is reached in 7 to 10 days. The setting time depends
on the type of cement, temperature, pressure, and the use of setting
accelerants. Excess pressure on the casing should be avoided during
the curing period so that the cement bond to the pipe is not disturbed.
Cement Integrity Log
Basics
Today’s
cement integrity logs come in four flavours: cement bond logs
(CBL), cement mapping logs (CMT), ultrasonic cement mapping tools
(CET), and ultrasonic imaging logs (USI, RBT). Examples and uses
for each are described in this Chapter.
Before
the invention of sonic logs, temperature logs were used to locate
cement top, but there was no information about cement integrity.
Some knowledge could be gained by comparing open hole neutron
logs to a cased hole version. Excess porosity on the cased hole
log could indicate poor fill-up (channels) or mud contamination.
The neutron log could sometimes be used to find cement top.
The
earliest sonic logs appeared around 1958 and their use for cement
integrity was quantified in 1962. The sonic signal amplitude was
the key to evaluating cement bond and cement strength. Low signal
amplitude indicated good cement bond and high compressive strength
of the cement.
In
the 1970’s, the segmented bond tool appeared. It uses 8
or more acoustic receivers around the circumference of the logging
tool to obtain the signal amplitude in directional segments. The
average signal amplitude still gives the bond index and compressive
strength, but the individual amplitudes are shown as a cement
map to pinpoint the location of channels, contamination, and missing
cement. This visual presentation is easy to interpret and helps
guide the design of remedial cement squeezes. An ultrasonic version
of the cement mapping tool also exists. The log presentation is
similar to the segmented bond log, but the measurement principle
is a little different.
Another
ultrasonic tool uses a rotating acoustic transducer to obtain
images for cement mapping. It is an offshoot of the open hole
borehole televiewer. The signal is processed to obtain the acoustic
impedance of the cement sheath and mapped to show cement quality.
The tool indicates the presence of channels with more fidelity
than the segmented bond tool and allows for analysis of foam and
extended cements.
Individual
acoustic reflections from the inner and outer pipe wall give a
pipe thickness log, helpful in locating corrosion, perforations,
and casing leaks.
Temperature Logs for Cement Top
In
the “good old days” before the invention of sonic
logs, there was no genuine cement integrity log. However, the
location of the cement top was often required, either to satisfy
regulations or for general knowledge. Since cement gives off heat
as it cures, the temperature log was used to provide evidence
that the well was actually cemented to a level that met expectations.
An example is shown at right. The top of cement is located
where the temperature returns to geothermal gradient. The log
must be run during the cement curing period as the temperature
anomaly will fade with time.
Today,
most wells are cemented to surface to protect shallow horizons
from being disturbed by crossflows behind pipe. In this case,
cement returns to surface are considered sufficient evidence for
a complete cement fill-up.
Cement Bond Logs (CBL)
Cement
bond logs (CBL) are still run today because they are relatively
inexpensive and almost every wireline company has a version of
the tool. The log example at the right illustrates the use of
the acoustic amplitude curve to indicate cement bond integrity.
The
examples in this Section are taken from ”Cement Bond Log
Interpretation of Cement and Casing Variables”, G.H. Pardue,
R.L. Morris, L.H. Gallwitzer, Schlumberger 1962.
EXAMPLE 1: CBL in well bonded cement – low amplitude means good
bond. The SP is from an openhole log; a gamma ray curve is more
common. Most logs run today have additional computed curves, as
well as a VDL display of the acoustic waveforms.
The CBL uses conventional sonic log principals of refraction to
make its measurements. The sound travels from the transmitter,
through the mud, and refracts along the casing-mud interface and
refracts back to the receivers, as shown in the illustration on
the left. In fast formations (faster than the casing), the signal
travels up the cement-formation interface, and arrives at the
receiver before the casing refraction.
The
amplitude is recorded on the log in millivolts, or as attenuation
in decibels/foot (db/ft), or as bond index, or any two or three
of these. A travel time curve is also presented. It is used as
a quality control curve. A straight line indicates no cycle skips
or formation arrivals, so the amplitude value is reliable. Skips
may indicate poor tool centralization or poor choice for the trigger
threshold.
The
actual value measured is the signal amplitude in millivolts. Attenuation
is calculated by the service company based on its tool design,
casing diameter, and transmitter to receiver spacing. Compressive
strength of the cement is derived from the attenuation with a
correction for casing thickness. Finally, bond index is calculated
by the equation:
1:
BondIndex = Atten / ATTMAX
Where:
Atten
= Attenuation at any point on the log (db/ft or db/meter)
ATTMAX
= Maximum attenuation (db/ft or db/meter)
The
maximum attenuation can be picked from the log at the depth where
the lowest amplitude occurs. On older logs attenuation and bond
index were computed manually. On modern logs, these are provided
as normal output curves. Bond Index is a qualitative indicator
of channels. A Bond Index of 0.30 suggests that only about 30%
of the annulus is filled with good cement.
INTERPRETATION
RULE 1: Low Amplitude = Good Cement
INTERPRETATION RULE 2: High Attenuation = Good Cement
INTERPRETATION RULE 3: High Bond Index = Good Cement
|
A
nomograph for calculating attenuation and bond index for older
Schlumberger logs is given below.
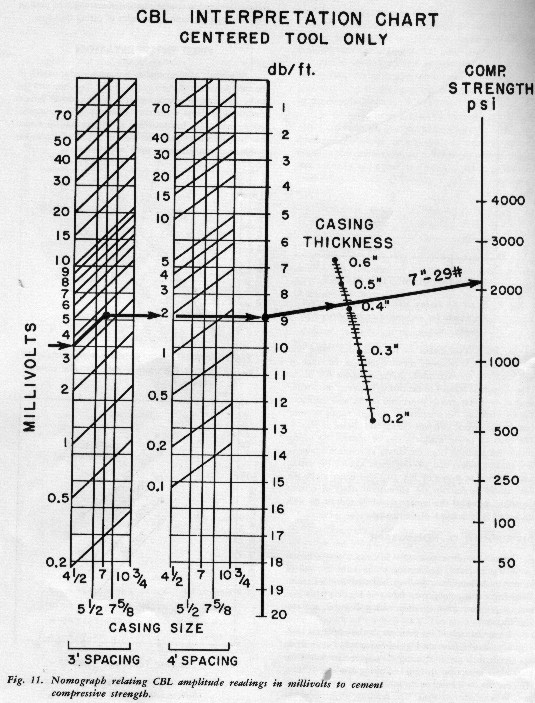
Chart for calculating cement bond attenuation
and cement compressive strength
Zone
isolation is a critical factor in producing hydrocarbons. In oil
wells, we want to exclude gas and water; in gas wells, we want
to exclude water production. We also do not want to lose valuable
resources by crossflow behind casing. Isolation can reasonably
be assured by a bond index greater than 0.80 over a specific distance,
which varies with casing size. Experimental work has provided
a graph of the interval required, as shown at the left.
The
following examples illustrate the basic interpretation concepts
of cement bond logs. Note that log presentations as clean and
simple as this are no longer available, but these are helpful
in showing the basic concepts.
EXAMPLE 2: CBL with both good and bad cement; hand calculated compressive
strength shown by dotted lines, labeled in psi; SP from openhole
log. Note straight line on travel time curve and bumps indicating
casing collars.
EXAMPLE
3: This log shows good bond over the oil and water zones,
but poor cement over the gas zone, probably due to percolation
of gas into the cement during the curing process. The worm holes
are almost impossible to squeeze and this well may leak gas to
surface through the annulus for life, because the bond is poor
everywhere above the gas. A squeeze job above the gas may shut
off any potential hazard.
EXAMPLE
4: Cement bond log before and after a successful cement squeeze.
Even though modern logs contain much more information than these
examples, the basics have not changed for 40 years.
Cement Bond Logs with
Variable Density Display (CBL-VDL)
While the important results of a CBL are easily seen on a conventional
CBL log display, such as signal amplitude, attenuation, bond index,
and cement compressional strength, an additional display track
is normally provided. This is the variable density display (VDL)
of the acoustic waveforms. They give a visual indication of free
or bonded pipe (as do the previously mentioned curves) but also
show the effects of fast formations, decentralized pipe, and other
problems.
But
you need really good eyes and a really good display to do this.
The display is created by transforming the sonic waveform at every
depth level to a series of white-grey-black shades that represent
the amplitude of each peak and valley on the waveform. Zero amplitude
is grey, negative amplitude is white, and positive amplitude is
black. Intermediate amplitudes are supposed to be intermediate
shades of grey.
This
seldom happens because the display is printed on black and white
printers that do not recognize grey. Older logs were displayed
to film that did not have a grey – only black or clear (white
when printed). So forget the grey scale and look for the patterns.
Older logs were analog – the wavetrain was sent uphole as
a varying voltage on the logging cable. These logs could not be
re-displayed to improve visual effects. Modern logs transmit and
record digitized waveforms that can be processed or re-displayed
to enhance their appearance.
The
examples below show the various situations that the VDL is supposed
to elucidate. These examples are taken from “New Developments
in Sonic Wavetrain Display and Analysis in Cased Holes”,
H.D. Brown, V.E. Grijalva, L.L. Raymer, SPWLA 1970.
INTERPRETATION
RULE 1: Low Amplitude = Good Cement
INTERPRETATION RULE 2: High Attenuation = Good Cement
INTERPRETATION RULE 3: High Bond Index = Good Cement
EXCEPT WHEN FAST FORMATION ARRIVALS APPEAR
|

EXAMPLE 5: CBL-VDL in free pipe (no cement). Notice straight
line and high amplitude pattern on VDL pipe arrivals (railroad
track pattern). Travel Time curve is constant and amplitude curve
reads high. Note casing collar anomalies on travel time and amplitude
curves, and more weakly on VDL display.
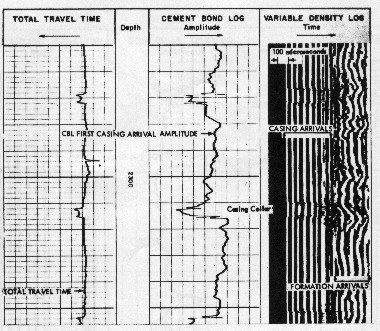
EXAMPLE 6: Casing is still unbonded (high amplitude railroad
tracks on early arrivals on VDL), amplitude curve reads high,
BUT late arrivals on VDL have “shape” and track porosity
log shape. This indicates free pipe laying on side of borehole
and touching formation. The VDL arrivals with “shape”
are the formation arrivals. Better casing centralization should
be used on the next well. A cement squeeze will improve the scene
but will probably not provide isolation on the low side of the
pipe.
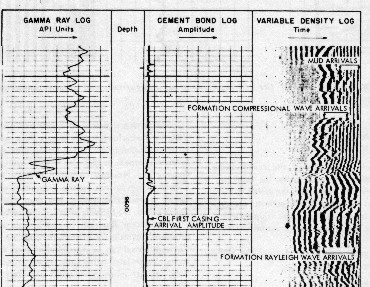
EXAMPLE 7: Well bonded pipe (low amplitude on early arrivals
on VDL, good bond to formation (high amplitude late arrivals with
“shape”). Mud arrivals would have high amplitude but
no “shape”.
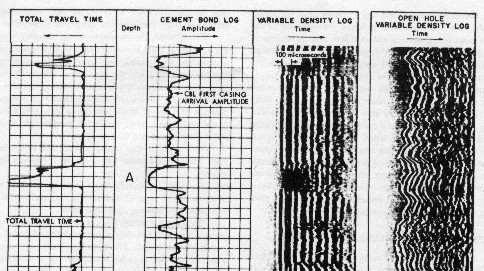
EXAMPLE 8: At Zone A, amplitude shows good bond, but VDL
shows low amplitude formation signal. This indicates poor bond
to formation. Travel time curve reads very high compared to baseline,
indicating cycle skipping on casing arrivals – but casing
bond is still good. Travel time less than base line value would
indicate fast formation. If you can detect fast formations, bond
is still good, regardless of high early arrival amplitude.
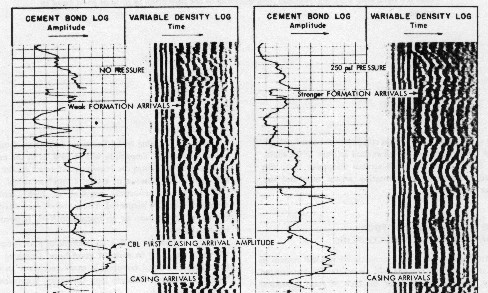
EXAMPLE 9: VDL on left shows poor bond but formation signal
is fairly strong. When casing is put under pressure, bond improves
(not a whole lot) as seen on lower amplitude early arrivals on
right hand log. This is called a micro-annulus. Under normal oil
production, the micro-annulus is not too big a problem unless
bottom hole pressure is very low. Micro-annulus is caused by dirty
or coated pipe, pressuring casing before cement is fully cured,
or ridiculous pressures applied during stimulation.
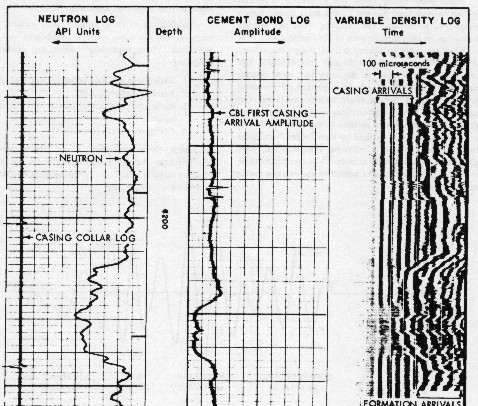
EXAMPLE 10: When there is no CBL-VDL made under pressure,
the un-pressured version can be used to interpret micro-annulus.
High amplitude early arrivals (normally indicating poor bond)
actually indicate good bond (with micro-annulus) IF formation
signals are also strong.
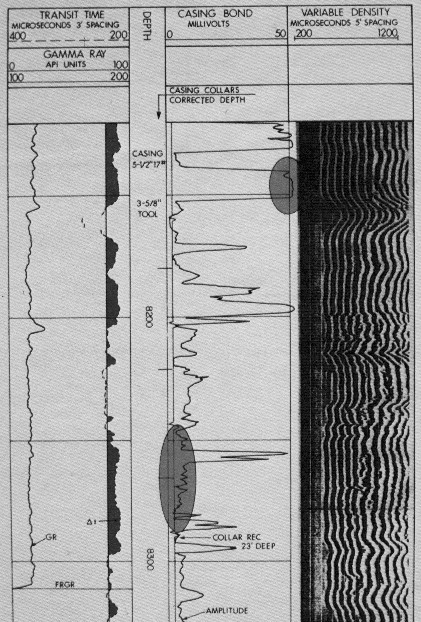
EXAMPLE 11: The travel time curve is lower than baseline (shaded
areas, Track 1) indicating fast formation arrivals. If you see
fast formation, you have a good bond to pipe and to formation.
However, you cannot use the amplitude curve (labeled “Casing
Bond” on this example) to calculate attenuation, compressive
strength, or bond index, because the amplitude is measured on
the formation arrivals, not the pipe arrivals.
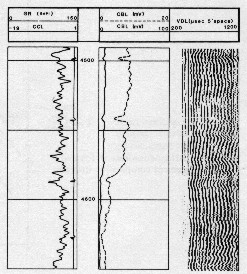
EXAMPLE 12: CBL-VDL shows the transition from normal to
foam cement just above 4650 feet. The foam cement has lower compressive
strength so the amplitude curve shifts to the right. Notice the
use of the expanded amplitude scale (0 to 20 mv) to accentuate
the change. The compressive strength is computed from a different
algorithm than normal cement, shown in the nomograph in below.
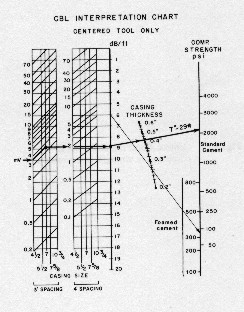
Nomograph for calculating compressive strength in normal and
foam cement.
Note
foam cement values on lower left side of compressive strength
scale.
Cement Mapping Tools (CET, PET, CMT)
Cement
evaluation (CET) and cement mapping (CMT) tools continue to use many
of the features of cement bond (CBL) logs, but add a new feature - a
circumferential image representing the cement quality, or lack of
it. The ultrasonic imaging (USI) tool, an offshoot of the openhole
acoustic image log, is the most recent version of this class.
The CET uses conventional sonic log principles, with measurements
made parallel to the tool axis, with 6 or 8 segmented transmitter
receiver sets spaced radial around the tool. CMT tools use an
ultrasonic pulse echo system, measuring radially, again with 6 or 8
radially spaced transducers. USI type tools use a rotating head,
pulse echo concept.
Classical cement bond (CBL) logging tools measure the amplitude
or attenuation of 20 to 30 kHz acoustic pulses propagating axially
along the casing between a single transmitter and a single receiver.
There
are three types of cement mapping tools. The CMT operates with
the same acoustic principles as the CBL, but uses oriented acoustic
receivers to recover amplitude data from 6, 8 , or ten radial
directions (depending on tool design). They may use a single transmitter
or one transmitter for each receiver. Some of these tools are
pad-type devices.
The
second type, the cement evaluation tool (CET) uses ultrasonic
acoustic pulses and measures radially instead of axially. This
tool is described later in this Section. A third type of cement
mapping tool, the rotating-head bond log (RBT) or ultrasonic imaging
log (USI) is described in the next Section.
On
a CMT, the average amplitude curve is used in the same manner
as a CBL to obtain attenuation, bond index, and cement compressive
strength. A cement map is made from the amplitude of the individual
receivers, to locate channels and voids in the cement.
These
logs are sometimes referred to generically as segmented cement
bond logs.
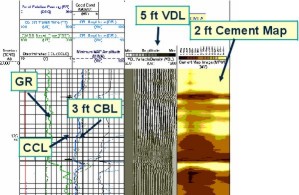
CBL-CMT log example
The
cement evaluation tool (CET) tool investigates the cement radially
instead of axially. Eight ultrasonic transducers, operating as
both transmitters and receivers, are positioned radially around
the CET sonde 45 degrees apart. Each transducer emits a beam of
ultrasonic energy in a 300 to 600 kHz band, which covers the resonant
frequency range of most oilfield casing thicknesses. These tools
are also called pulse echo tools (PET).
CET
log presentations look similar to the CMT, but casing diameter
and other information is obtained by processing the echo signal.
The pulse echo concept is illustrated below.
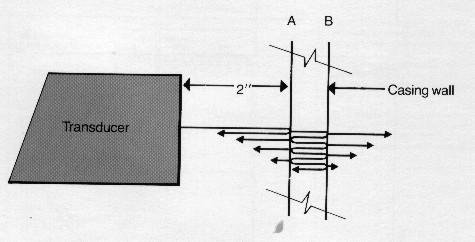
Sound paths for pulse echo (CET) type cement
bond log
The
energy pulse causes the casing to ring or resonate in its thickness
dimension, as shown above, perpendicular to the casing
axis. The vibrations die out quickly or slowly, depending on the
material behind the casing. The majority of the energy is reflected
back to the transducer where it is measured, and the remainder
passes into the casing wall and echoes back and forth until it
is totally attenuated.
Each
time the pulse is reflected off the inner casing wall, some energy
passes through the interface and reaches the transducer. A ninth
transducer continually measures acoustic travel time of the casing
fluid column so that the other eight transducer travel times can
be converted to distance measurements. This fluid travel time
can be presented on the log, if desired, to indicate the type
of casing fluid.
CET
logs record attenuation of the acoustic signal directly by computing
the decay of energy on each waveform by comparing the energy in
an early-time window W1 and a later-time window W2, as shown
below.
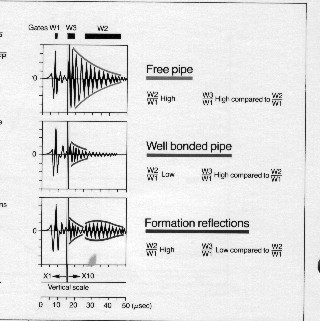
Reflection waveforms and measurement gates for CET calculations
INTERPRETATION
RULE 1: Low Amplitude = Good Cement
INTERPRETATION RULE 2: High Attenuation = Good Cement
INTERPRETATION RULE 3: High Bond Index = Good Cement
INTERPRETATION RULE 4: High Compressive Strength = Good
Cement |
Minimum
and maximum compressive strength are computed from the minimum
and maximum attenuations on the 8 transducers. These are displayed
as continuous log curves. The cement map is created from the energy
of the early arrivals of the acoustic waveform in the 8 radial
directions. A gas flag is generated when late arrivals are very
low energy and a fast formation flag is generated when late arrivals
are high energy.
The
tool can be oriented to the low side of the borehole or to true
north. In addition, measurements of casing diameter, casing roundness,
and tool eccentering are derived from the arrival times of the
8 transducers. These caliper curves show casing wear, corrosion,
or collapse.
Experience
has shown that when there is good cement around the pipe, the
bond to the formation is usually good, too. When the cement sheath
is very thin, the CET tool responds to formation arrivals. However,
when the cement is thick the formation reflections may be too
small to measure. So, if good pipe bond but bad formation bond
is suspected, the best interpretation can be made by combining
the Cement Evaluation log with the Cement Bond/Variable Density
log.
eXAMPLES
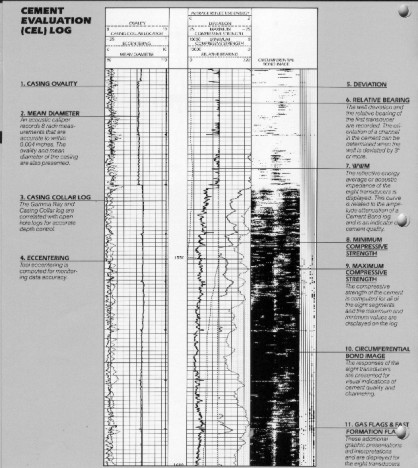
Layout of CET log. The important curves are
the attenuation and compressive strength values
in Track 2 and
the cement map in Track 3. Other data is annotated on the side
of the plot.
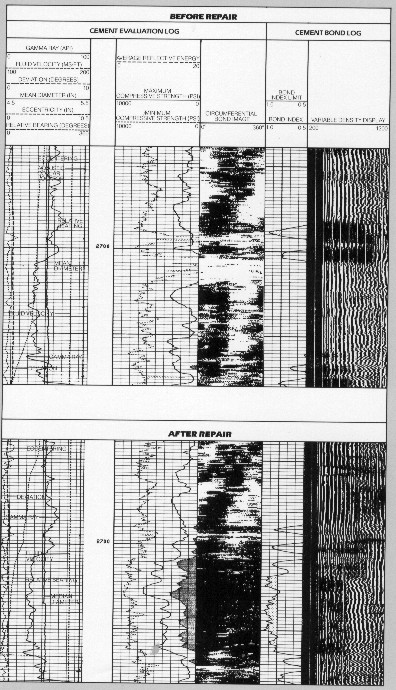
CET with CBL-VDL before and after squeeze. Note
improved cement map, higher
compressive strength, and formation
signal on VDL.
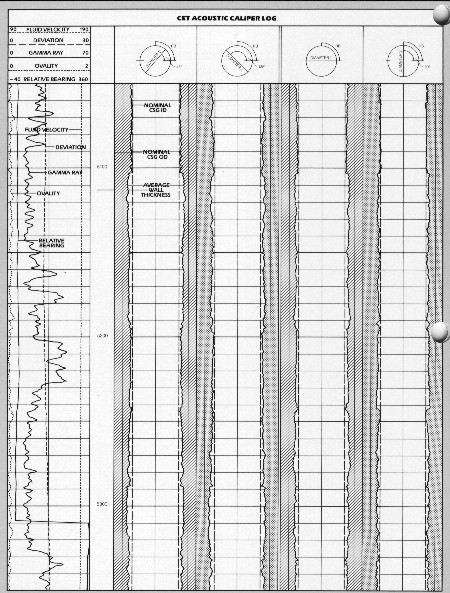
Casing diameter, casing thickness, and ovality
logs from CET tool are use for casing inspection.
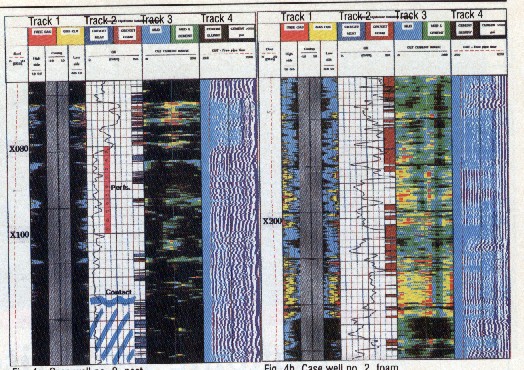
Data from CBL-VDL and CET are combined in Schlumberger’s
Cement Advisor program to
generate a more informative cement map
and zone isolation flags (Track 2) in both neat and
foam cement.
A section of well with neat cement is shown at left and a section
of foam cement
on the right. Track 1 contains colour coded cement
volume map and Track 3 shows a
computed cement impedance map.
The colour code is dark for good cement shading to
yellow for
gas (nitrogen in the case of foam cement). Colour code thresholds
vary from job to job.
Ultra Sonic Image Logs (USI, RBT)
The USI Ultra Sonic Imager and UBI Ultrasonic Borehole Imager
tools are acoustic borehole imaging logs. The USI is a cased
hole cement bond / cement mapping tool with output similar to
the CET, but with more complete coverage of the borehole. The
UBI is an openhole tool for formation imaging. They are physically
similar to each other but use different transducers. This tool
type is sometimes referred to as a rotating-head bond tool (RBT).
In
addition, precise acoustic measurements of the internal dimensions
of the casing and of its thickness provide a map-like presentation
of casing condition including internal and external damage or
deformation.
Rotating head ultrasonic (acoustic) imaging tools are the current
state of the art for cement and casing integrity mapping. The
rotating head gives greater circumferential resolution than the
segmented CET and CMT class of tools. The casing inspection
capability cannot be accomplished by other cement evaluation tools.
The
sonde includes a rotating transducer subassembly available in
different sizes to log all normal casing sizes. The direction
of rotation of the subassembly controls the orientation of the
transducer – counterclockwise for the standard measurement
mode (transducer facing the casing or the borehole wall), and
clockwise to turn the transducer 180 degrees within its subassembly
(transducer facing a reflection plate within the tool) to measure
downhole fluid properties. The fluid properties are used to correct
the basic measurements for environmental conditions.
Analysis
of the reflected ultrasonic waveforms provides information about
the acoustic impedance of the material immediately behind the
casing. A cement map presents a visual indicator of cement quality.
Impedance is measured in units of megaRayls.
INTERPRETATION
RULE 1: Low Amplitude = Good Cement
INTERPRETATION RULE 2: High Attenuation = Good Cement
INTERPRETATION RULE 3: High Bond Index = Good Cement
INTERPRETATION RULE 4: High Compressive Strength = Good
Cement
INTERPRETATION RULE 5: High Acoustic Impedance = Good Cement |
RAYL:
A unit of specific acoustic impedance in the centimeter-gram-second
system of units, = 10 pascal-seconds per meter. A specific
acoustic impedance has a magnitude of 1 rayl when a sound
pressure of 1 microbar produces a linear velocity of 1 centimeter
per second. The unit is named for John William Strutt, third
Lord Rayleigh (1842-1919). |
Like
the CET, the USI tool analyzes the decay of the thickness-mode
resonance signal contained in the reflected acoustic pulse, but
the analysis is performed in a different manner. The CET tool
has eight fixed transducers in a helical array, 45 degrees apart
azimuthally each seeing only a small segment of the casing. The
USI tool has a single rotating transducer that looks all around
the casing.
As
the acoustic impedance of the casing material and of the borehole
fluid are essentially constant, the signal inside the casing decays
at a rate that is dependent on the acoustic impedance of the material
outside the casing.
In
contrast to CET processing, which uses traditional energy windows,
USI processing derives acoustic impedance directly from the fundamental
resonance to measure the following:
1.
The acoustic impedance of the cement or whatever material is between
the casing and the formation.
2.
Casing thickness from the natural resonant frequency of the casing,
which is approximately inversely proportional to the wall thickness.
3.
Internal casing radius. The time between the firing and the major
peak of the echo is measured by locating the waveform peaks. Time
is converted to a measurement of the internal radius using the
fluid properties measurement to compute the velocity of sound
in mud, taking into account the transducer’s own dimensions.
4.
Casing inspection. The inside and outside diameters are determined
from the transit time and casing thickness measurements. The maximum
amplitude of the waveform provides a qualitative measure of the
internal surface rugosity of the casing.
Several
presentations are available to address specific applications.
Negative conditions are indicated by the color red. For example,
red curves represent outputs for tool eccentering, minimum amplitude,
maximum internal radius, minimum thickness, gas index, and so
on. Increasing intensity of red in the images represents increasingly
negative conditions such as low amplitude, metal loss, and the
presence of gas in the cement map. The gas may be intentional,
as in foam cement, or unintentional from gas invasion as the cement
cures.
The
following log presentations are available from USI recordings:
1.
Fluid properties presentation, including fluid acoustic velocity,
acoustic impedance of fluid, and thickness of reference calibrator
plate.
2.
Cement Presentation, including cement properties curves, cement
map, and casing dimensions, plus synthetic bond index and minimum,
maximum and average values of acoustic impedance. Two cement images
are generated, one with and one without impedance thresholds.
3.
Corrosion Presentation with casing profile, casing reflectivity,
casing Internal radii, thickness image, Internal and external
radii, average and maximum thickness,
4.
Composite Presentation, with cement, corrosion measurements, and
processing flags. Two acoustic impedance images are presented:
one on a linear scale and one with thresholds corresponding to
the acoustic impedance of gas and mud.
5.
Impedance Images:
Linear color scale
White < 0.5 MRayl = no cement.
Colors from yellow to brown represent steps of 0.5 MRayl.
Black < 8 MRayl - good cement.
With
thresholds
Red < 0.3 MRayl = gas intrusion
from formation or gas breakout
in foam cement.
Blue < 2.6 MRayl = fluid – water
or mud in cement.
Yellow < 3 MRayl = foam cement
or very contaminated neat
cement.
Colors from yellow to brown represent steps of 0.5 MRayl and indicate
solids, eg. Cement or cement extenders.
Black < 8 MRayl = high quality neat cement.
These
thresholds can be varied for conditions such as light cement (where
lower acoustic impedance indicates lower fluid cutoff) and heavy
mud (with a higher fluid threshold cutoff). Check the colour scale
on each log.
6.
Amplitude images:
The amplitude image, derived from the amplitude of the main echo
of each waveform, represents the reflectivity of the internal
surface of the casing. The image is normalized with respect to
the maximum value at a given depth, and all points are presented
in terms of attenuation from the maximum amplitude at that depth.
Normalized minimum amplitude curves are plotted.
Linear
color scale
Black = low signal (-6 dB) = good bond
Colors from dark red to white represent steps of 0.5 dB
White = high signal (0 dB) = no bond
7.
Diagnostic images:
Processing flags – diagnostics for the field engineer.
8.
Internal radius images:
The internal radius image shows the variations around IRAV, the
average
radius at each depth. Two color scales are used – blue to
white for
internal radii less than IRAV and white to red for internal radii
greater
than IRAV. Each color step represents 0.008 in.
9.
Thickness images:
The thickness image shows the variations around THAV, the average
value of the thickness at each depth. Two color scales are used
– red
to white for thicknesses less than THAV and white to blue for
thicknesses
greater than THAV.
Alternate
images that plot internal radius and thickness versus API specifications
of the casing are available.
The
acoustic impedance of the mud must be accurately known to within
10 percent in order to obtain a 0.5-MRayl accuracy in cement.
The acoustic impedance of the mud is provided by the downhole
fluid properties measurement, which is normally acquired while
tripping into the well.
A
microannulus affects the apparent cement acoustic impedance. Laboratory
experiments show that a 100-micron (0.004 inch) microannulus results
in a 50 percent loss in apparent impedance. Even the smallest
liquid-filled microannulus causes the loss of shear coupling into
the cement and a drop of approximately 20 percent in impedance.
Whenever the presence of a microannulus is suspected, the USI
tool should be run under pressure to obtain an improved acoustic
impedance measurement.
A
dry microannulus is called micro-debonding and gives a patchy
looking cement image.
The
USI tool can resolve the impedance of the material filling a channel
down to 1.2 inches, which is therefore the minimum quantifiable
channel size. The angular resolution improves for larger diameter
casing, from 30 degrees in 4.5-in. casing to 10 degrees in 13
3/8-in. casing. However, interpretation is required since channels
are not always surrounded by high-impedance cement nor are they
always filled with low impedance material.
EXAMPLES
The
following examples are courtesy of Schlumberger.
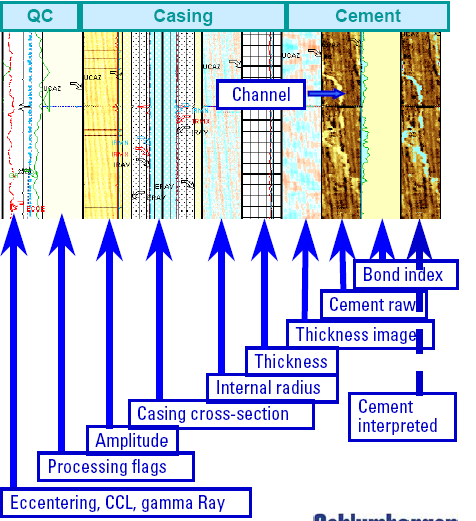
Typical USI composite presentation with cement
images, synthetic bond index, and casing image.
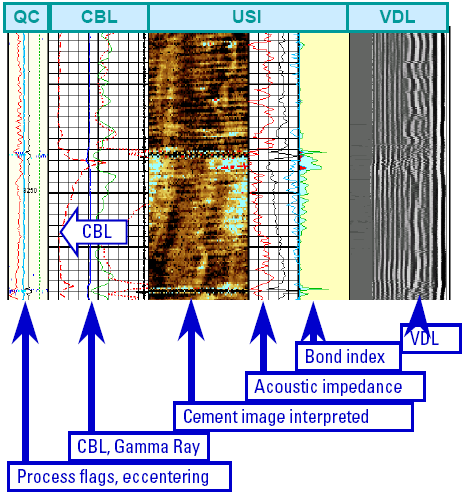
Combination of USI and CBL-VDL gives more complete
picture – high resolution from USI and formation arrivals
on VDL.
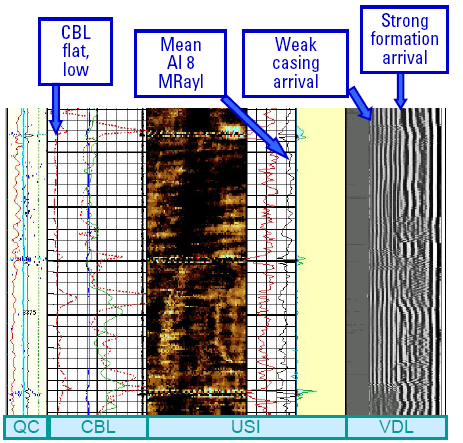
Good cement – low amplitude on CBL, high Acoustic
Impedance on USI, no serious channels on image.
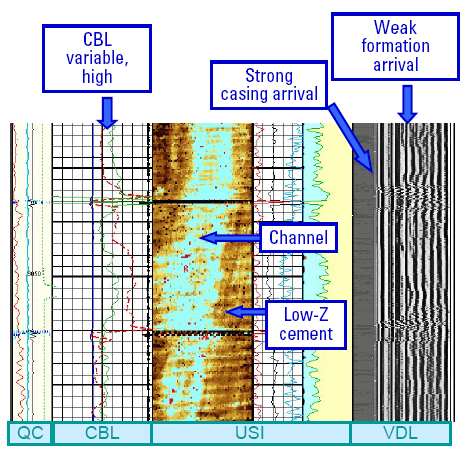
Poor cement – high amplitude on CBL, low
Acoustic Impedance (blue colour) on image indicates large void
space filled with liquid (mud).
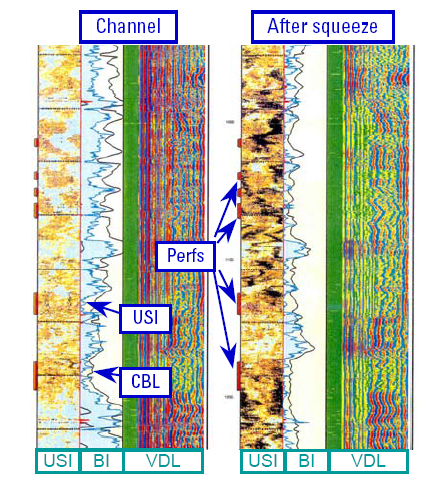
USI-VDL and USI before and after squeeze.
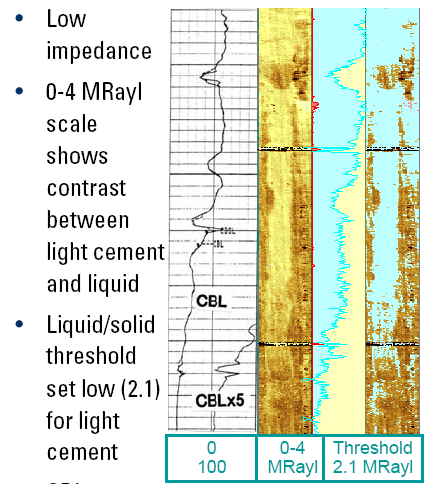
CBL and USI in foam cement.
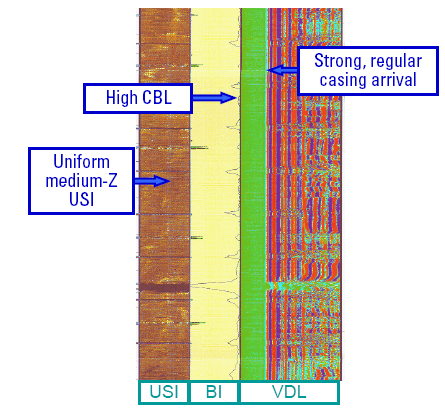
Microannulus – high amplitude on CBL and
VDL, medium to high acoustic impedance on USI.
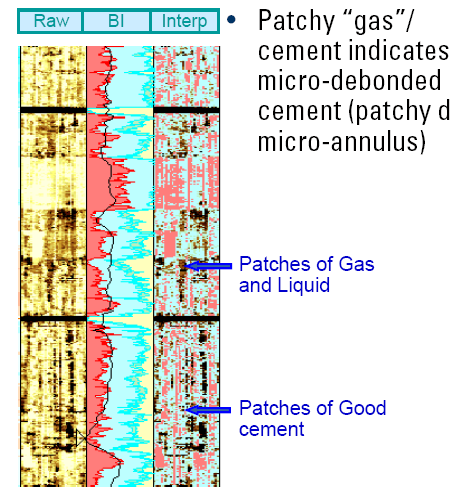
Micro-debonding – similar to microannulus
but patchy instead of continuous.
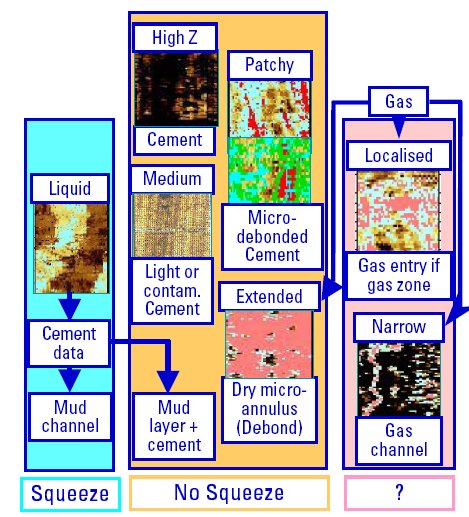
Samples of cement jobs with problems, and possible
cures.
|