CONVENTIONAL
CORING METHODS
Porosity, permeability, grain density, and
mineralogy of reservoir rocks are important elements in a reservoir
description. We can estimate these properties from well logs or
measure them from rock samples in the laboratory. The rock samples
are obtained by cutting a piece of rock from the well bore; the
process is called coring.
Conventional cores are cut using a specialized subassembly at the
bottom of the drill string. This consists of a coring drill bit
(usually a diamond bit), a core barrel to hold the recovered core,
and fingers in the core barrel to hold the core in place while the
coring assembly is pulled out of the hole. At the surface, the core
is retrieved from the core barrel and placed in transport boxes,
which are transported to a laboratory for further study.
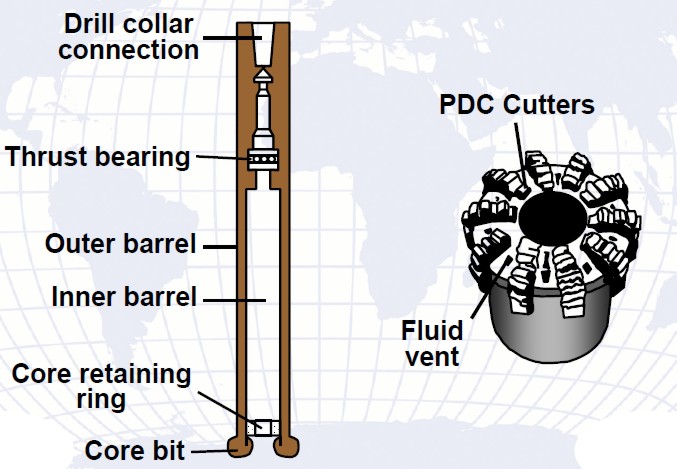
Coring assembly on bottom of drill string and coring bit
SIDEWALL CORING
If coring while drilling is impractical, small cores can be taken
on wireline using a sidewall core gun or a sidewall rotary coring
tool. The sidewall core gun uses black powder explosives to fire a
steel bullet into the rock adjacent to the toole. The hollow bullet
captures a small piece of rock that is pulled to the surface by the
tool. Such guns can recover up to 48 samples in one trip in the
hole. Depth control is monitored using a gamma ray log to correlate
to previous logs run in the well.
The rotary coring tool uses an electrically driven diamond
bit to drill a small core from the formation adjacent to the tool.
Several cores can be taken at different depths before the tool is
brought to the surface.
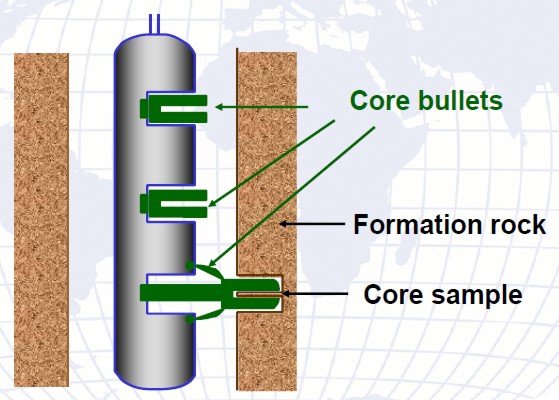
Rotary core drill on wireline
Sidewall core gun with steel bullets
SELECTING CORE PLUG LOCATIONS
Most routine core analysis is
oerformed on core plugs drilled from slabbed or whole core.
Plugs are 1.0 to 1.5 inches in diameter and 2 to 3 inches long.
Locations for each plug are selected based on visual observation
of changes in rock texture, porosity, or lithology / mineralogy,
giving rise to irregular intervals between core plugs. Some
operators prefer equal intervals b etween samples.
The orientation of the core plug relative to the core axis and
bedding dip angle is important. Horizintal rock properties are
determined from plugs drilled parallel to bedding, not at right
angles to the core's verical axis. Likewise, plugs for vertical
properties are taken perpendicular to bedding planes.
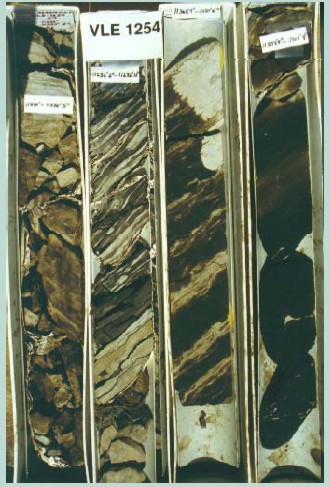
Core slab, core plug, full diameter, and whole core
definition
Core photo of slabbed core
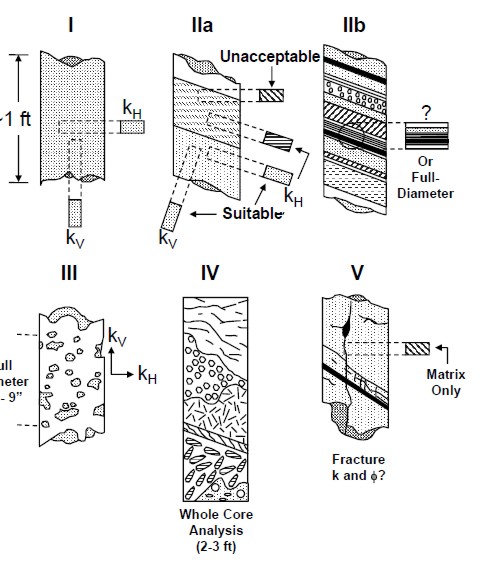
Taking core plugs for horizontal and vertical rock properties
requires care and attention to dipping beds, fractures,
lithology variations, and porosity heterogeneity. Do NOT
high-grade the selection of core plugs by choosing only good
porosity points - this will not provide useful information to
control petrophysical evaluations, reserves, productivity or
other performance calculations.
CORE
CLEANING METHODS
Before measuring porosity and permeability, the core samples must be
cleaned of residual fluids using solvents, then thoroughly dried.
There are numerous lab techniques available to do this. Most methods
also provide the oil and water saturation of the core samples on an
“as-received” basis.
The number of cycles or amount of solvent which must be used depends
on the nature of the hydrocarbons being removed and the solvent
used. Often, more than one solvent must be used to clean a sample.
The solvents selected must not react with the minerals in the core.
Toluene and benzene are most frequently used to remove oil and
methanol and water is used to remove salt from interstitial or
filtrate water. The cleaning procedures used are specifically
important in special core analysis tests, as the cleaning itself may
change wettability.
The core sample is dried to remove connate water from the pores,
or to remove solvents used in cleaning the cores. When hydratable
minerals are present, the drying procedure is critical since
interstitial water must be removed without mineral alteration.
Drying is commonly performed in a regular oven or a vacuum oven at
temperatures between 500C to 1050C. If problems with clay are
expected, drying the samples at 600C and 40 % relative humidity will
not damage the samples.
Direct Injection of Solvent
The solvent is injected into the sample in a continuous process. The
sample is held in a rubber sleeve thus forcing the flow to be
uniaxial.
Centrifuge Flushing
A centrifuge which has been fitted with a special head sprays warm
solvent onto the sample. The centrifugal force then moves the
solvent through the sample. The used solvent can be collected and
recycled.
Gas Driven Extraction
The sample is placed in a pressurized atmosphere of solvent
containing dissolved gas. The solvent fills the pores of sample.
When the pressure is decreased, the gas comes out of solution,
expands, and drives fluids out of the rock pore space. This process
can be repeated as many times as necessary.
Soxhlet Extraction
A Soxhlet
extraction apparatus is the most common method for cleaning samples,
and is routinely used by most laboratories.
Soxhlet (left) and Dean-Stark (right) extraction apparatus
As
shown in the illustration, toluene is brought to a slow boil in a
Pyrex flask; its vapors move upwards and the core becomes engulfed
in the toluene vapors at approximately 1100C. Eventually, water
within the core sample in the thimble will be vaporized. The toluene
and water vapors enter the inner chamber of the condenser, the cold
water circulating about the inner chamber condenses both vapors to
immiscible liquids. Recondensed toluene together with liquid water
fall from the base of the condenser onto the core sample in the
thimble; the toluene soaks the core sample and dissolves any oil
with which it come into contact.
When the liquid level within the Soxhlet tube reaches the top of the
siphon tube arrangement, the liquids within the Soxhlet tube are
automatically emptied by a siphon effect and flow into the boiling
flask. The toluene is then ready to start another cycle.
A complete extraction may take several days to several weeks in the
case of low API gravity crude or presence of heavy residual
hydrocarbon deposit within the core. Low permeability rock may also
require a long extraction time.
Dean-Stark Distillation-Extraction
The Dean-Stark distillation provides a direct determination of water
content. The oil and water area extracted by dripping a solvent,
usually toluene or a mixture of acetone and chloroform, over the
plug samples. In this method, the water and solvent are vaporized,
recondensed in a cooled tube in the top of the apparatus and the
water is collected in a calibrated chamber (Figure 2.1b).
The solvent overflows and drips back over the samples. The oil
removed from the samples remains in solution in the solvent. Oil
content is calculated by the difference between the weight of water
recovered and the total weight loss after extraction and drying.
Vacuum Distillation
The oil and water content of cores may be determined by this method.
As shown in Figure 2.2, a sample is placed within a leakproof vacuum
system and heated to a maximum temperature of 2300C. Liquids within
the sample are vaporized and passed through a condensing column that
is cooled by liquid nitrogen.
Summary
The direct-injection method is effective, but slow. The method of
flushing by using centrifuge is limited to plug-sized samples. The
samples also must have sufficient mechanical strength to withstand
the stress imposed by centrifuging. However, the procedure is fast.
The gas driven-extraction method is slow. The disadvantage here is
that it is not suitable for poorly consolidated samples or chalky
limestones.
Distillation in a Soxhlet apparatus is slow, but is
gentle on the samples. The procedure is simple and very accurate
water content determination can be made. Dean-Stark method crushes
the sample, so it cannot be used for other purposes, but accurate
oil, water, and pore volumes can be determined. However, if
clay bound water is present some or all of it may be driven off,
adding to the water recovered from the pore space.
Vacuum distillation is often used for full diameter cores because
the process is relatively rapid. Vacuum distillation is also
frequently used for poorly consolidated cores since the process does
not damage the sample. The oil and water values are measured
directly and independently of each other.
|